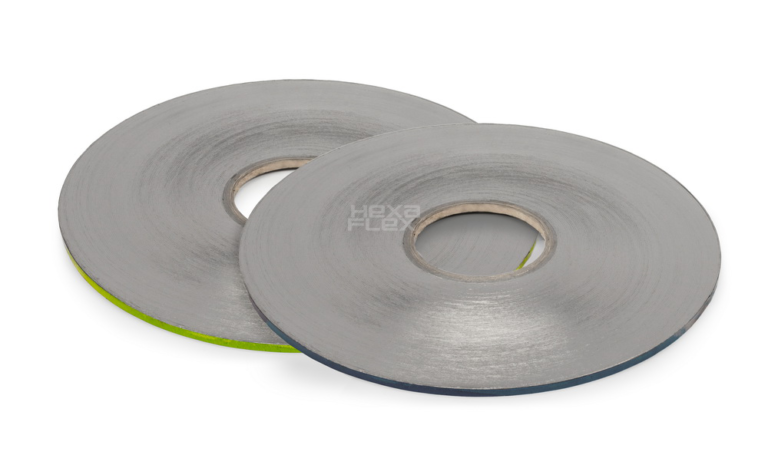
Hexaflex™ slit tapes are manufactured with the use of a whole range of Hexaflex™ graphite foils which can further be cut to any required width upwards 4 mm / 1/8 ” with high precision which makes it an excellent filler for production of high-quality spiral wound gaskets and graphite die-molded rings.
Due to special patented technology, Hexaflex™ tapes could be produced with high strength which solves the critical and nagging problem of breaking-up of filler for SWG’s and graphite rings production, and lets your production line work without hiccups of frequent stoppage. This has often led to increase of plant efficiency by significant measures. Higher OEE gives much higher returns while comparing with cheaper materials. Highest quality of raw materials leads to lower downtime and consistent finished products.
Huge length of winding (up to 100m / 330’) makes possible longer continuous production and manufacturing of large diameter SWG’s.
APPLICATIONS:
MAIN FEATURES AND PROPERTIES:
- Huge length of winding (up to 100m / 330’);
- Consistently accurate width and high strength;
- Resistance to high temperatures;
- Impermeability to gases and fluids;
- Zero sulphur and halogen content;
- Anti-sticking properties in accordance with ASTM F607;
- Fire-safety approved (API Specification 6FB – Hexaflex™ Σ Sigma);
- Absence of binders.
FORMS OF SUPPLY:
Thickness …………..………….. 0.38, 0.5, 0.76 mm / .015, .020, .030”
Width ……………………………4.0 – 130 mm / 1/8 – 5”
Length of winding ……………… 30, 50, 60, 90, 100 m / 100, 165, 200, 330’
Density …………………………. 1.0, 0.7, 1.12 g/cc / 62, 44, 70 lb/ft3
AVAILABLE OPTIONS OF GRAPHITE FOIL HEXAFLEX™
Parameter | Grade Β Beta Industrial | Grade Γ Gamma High-purity | Grade Δ Delta Ultra-high purity | Grade Σ Sigma Anti-oxidation and | Grade Θ Theta High-purity and oxidation resistant | Grade 1Θ 1Theta Ultra-low losses |
Carbon, % | > 98,0 | > 99,0 | > 99,85 | > 98,0 (99,0*) | > 99,0 | > 98,0 |
Ash, % | < 2,0 | < 1,0 | < 0,15 | < 2,0 | < 1,0 | < 2,0 |
Sulfur, ppm | < 200 | < 100 | < 50 | < 100 | < 100 | < 100 |
Chlorine**, ppm | < 40 | < 40 | < 20 | < 40 | < 20 | < 20 |
Fluorine**, ppm | < 20 | < 10 | < 10 | < 10 | < 10 | < 10 |
Total halogens (Cl+F+Br)** , ppm | < 200 | < 100 | < 50 | < 200 | < 100 | < 100 |
Tensile strength, MPa | > 4,5 (> 700 psi) | > 4,5 (> 700 psi) | > 4,0 (> 700 psi) | > 5,0 (> 725 psi) | > 5,0 (> 725 psi) | > 5,0 (> 725 psi) |
Compressibility, % | > 40 | > 40 | > 40 | > 40 | > 40 | > 40 |
Recoverability, % | > 10 | > 10 | > 9 | > 10 | > 10 | > 10 |
Oxidation and corrosion inhibitor | – | – | – | yes | yes | yes |
Weight loss (670 °C / 1238 °F), %/h | < 12 | < 12 | – | < 4 | < 3 | < 1 |
Compliance to special requirements | DVGW DIN 3535-6 | BAM; ASTM F2168 class 2 (B); DIN 3535-6 | PMUC norms; GS RC PVE 011; BAM; ASTM F2168 class 2 (B); DIN 3535-6 | MESC 85/203; EN 14772 §6.7; ASTM F2168 class 2 (A); DIN-28091-4; DIN 3535-6 | MESC 85/203; EN 14772 §6.7; ASTM F2168 class 2 (A); DIN-28091-4; DIN 3535-6 | MESC 85/203; EN 14772 §6.7; ASTM F2168 class 2 (A); DIN-28091-4; DIN 3535-6 |
* initial carbon content (before inhibitors added)
**leachable
